薄膜電路技術(shù)在T/R組件中的應(yīng)用
1.引言
本文引用地址:http://www.ex-cimer.com/article/165464.htm采用薄膜技術(shù)來(lái)制造薄膜電路是薄膜領(lǐng)域中一個(gè)重要分支。薄膜電路主要特點(diǎn):制造精度比較高(薄膜線寬和線間距較小),可實(shí)現(xiàn)小孔金屬化,可集成電阻、電容、電感、空氣橋等無(wú)源元件,并且根據(jù)需要,薄膜電路可以方便地采用介質(zhì)制造多層電路。薄膜多層電路是指采用真空蒸發(fā)、濺射、電鍍等薄膜工藝以及濕法刻蝕和干法刻蝕(反應(yīng)離子刻蝕、等離子刻蝕、激光刻蝕)等圖形形成技術(shù),在拋光的基板(陶瓷、硅、玻璃等材料)上制作導(dǎo)體(Cu或Au等)布線與絕緣介質(zhì)膜(PI或BCB等)相互交疊的多層互連結(jié)構(gòu)。
薄膜多層電路技術(shù),由于具有互連密度高、集成度高、可以制造高功率電路、整個(gè)封裝結(jié)構(gòu)具有系統(tǒng)級(jí)功能等突出特點(diǎn),在微波領(lǐng)域的應(yīng)用很有競(jìng)爭(zhēng)力,特別是在機(jī)載、星載或航天領(lǐng)域中,其體積小、重量輕、可靠性高的特點(diǎn)更加突出,是一種非常有潛力的微波電路模塊(低噪聲放大器、濾波器、移相器等)、甚至需求量越來(lái)越大的T/R組件基板制造技術(shù)。
本文將在分析薄膜電路在T/R組件中應(yīng)用的特點(diǎn)的基礎(chǔ)上,介紹幾種典型的應(yīng)用實(shí)例,并給出發(fā)展建議。
2. 薄膜電路技術(shù)在T/R組件中應(yīng)用的特點(diǎn)分析
隨著雷達(dá)技術(shù)的發(fā)展,有源相控陣?yán)走_(dá)成為主流,而其核心則是T/R組件,通常每部雷達(dá)含有成千上萬(wàn)只T/R組件。T/R組件不論其使用頻率是否相同,也不論其使用場(chǎng)合是否相同,其基本構(gòu)成是相同的,主要是由功率放大器、驅(qū)動(dòng)放大器、T/R開(kāi)關(guān)、移相器、限幅器、低噪聲放大器、環(huán)流器、邏輯控制電路等組成,其結(jié)構(gòu)框圖如圖1所示(1)。這些基本構(gòu)成,在工藝實(shí)現(xiàn)時(shí),部分可以直接做在電路板上,如微帶傳輸線、開(kāi)關(guān)、耦合器、濾波器等,部分采用外貼芯片(如功放、驅(qū)放等)、電容、環(huán)流器等來(lái)實(shí)現(xiàn)。因此,從使用功能和結(jié)構(gòu)上,T/R組件實(shí)際上可以看作是一種具有收發(fā)功能的微波多芯片模塊。
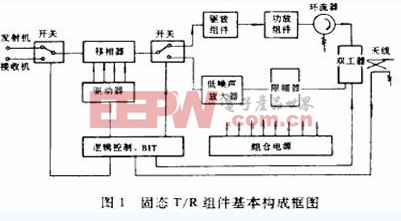
受雷達(dá)波束柵瓣效應(yīng)(相鄰兩個(gè)輻射單元的中心距小于工作波長(zhǎng)的一半)以及重量、成本等限制,T/R組件的小型化、集成化、輕量化將是其發(fā)展趨勢(shì)。為了滿足其性能要求,采用低溫共燒陶瓷LTCC、高溫共燒陶瓷HTCC、薄膜多層電路技術(shù)、多層微波印制電路技術(shù)等多層集成技術(shù)來(lái)研制和生產(chǎn)T/R組件成為必然選擇,幾種多層技術(shù)的比較見(jiàn)表1(2~3)。

從表中可以看出,薄膜多層互連基板,具有如下突出優(yōu)點(diǎn):
(1)布線密度高,體積可以很小、重量很輕;
(2)集成度高,可以埋置電阻、電感、電容等無(wú)源器件以及有源芯片;
(3)高頻特性好,可用于微波及毫米波領(lǐng)域;
(4)承受功率密度高,可選用高導(dǎo)熱的金屬、金剛石、陶瓷或鋁炭化硅復(fù)合材料等作基板,制造高密度高功率多層基板。
薄膜多層互連基板與其它類(lèi)型的基板相比,具有如下明顯的缺點(diǎn):
(1)工藝采用串形方式,成品率相對(duì)低,制造成本高;
(2)制造層數(shù)受限制。
薄膜多層電路技術(shù)由于具有明顯的優(yōu)點(diǎn)和缺點(diǎn),因此在制造T/R組件的選擇上,可以有兩種方案。第一,可以采用薄膜技術(shù)在陶瓷基板或金屬基板上直接制造T/R組件(4~5),發(fā)揮薄膜高精度、高集成度、高功率的性能,這種方法成本較高; 第二,將薄膜技術(shù)和其他多層電路技術(shù)(如厚膜技術(shù)、HTCC、LTCC等)結(jié)合起來(lái)(6-8),制造T/R組件,揚(yáng)長(zhǎng)避短,既發(fā)揮其他基板容易實(shí)現(xiàn)多層的特點(diǎn),從而克服薄膜技術(shù)本身制造層數(shù)不足的缺點(diǎn),又能發(fā)揮薄膜技術(shù)本身的高精度、高性能特長(zhǎng)。
3. 薄膜技術(shù)在T/R組件中應(yīng)用實(shí)例
3.1 陶瓷基板上薄膜混合集成T/R組件
RCA實(shí)驗(yàn)室在1985年報(bào)道了在高導(dǎo)熱陶瓷BeO基板上采用薄膜工藝制造的T/R組件(3),尺寸為7.0cm×9.0cm×1.6cm,工作頻率16.0~16.5GHz,峰值功率3.9~4.4 W,電壓調(diào)諧范圍2.5~2.9,噪聲系數(shù)5dB。
Martin Marietta實(shí)驗(yàn)室,1995年首次報(bào)道了采用薄膜技術(shù)制造了頻率高達(dá)94GHz 的W波段的8單元T/R組件(4),如圖3所示。組件的尺寸16.5mm×28.3cm×1.8 cm,最大增益47.8 dB。主要工藝為:先在0.5毫米厚的鉬基片上,采用銅導(dǎo)體和聚酰亞胺的薄膜多層工藝制造直流和控制信號(hào)主板,然后在0.125mm厚的低損耗Al2O3陶瓷板上用薄膜工藝制造RF傳輸線,最后將RF部分和芯片、電容等裝配在低頻主板上。
3.2 金屬基板上薄膜混合集成T/R組件
在鋁、鉬等金屬基板上制作T/R組件或多芯片模塊,近年來(lái)也有不少報(bào)道(4~6)。1995年,澳大利亞的O.Sevimli報(bào)導(dǎo)了一種金屬基V波段(可以達(dá)110GHz以上)薄膜多層多芯片組件專利技術(shù)(5),結(jié)構(gòu)示意圖見(jiàn)圖2。這種技術(shù)工藝過(guò)程是這樣的:首先是在金屬基板上腐蝕出用于安放芯片的孔,然后把芯片采用導(dǎo)電膠固定在孔內(nèi),控制好安裝芯片的孔的深度使芯片與金屬表面在同一平面內(nèi)并精確定位,表面涂敷一層適于毫米波領(lǐng)域使用的BCB等介質(zhì)材料,最后在芯片焊盤(pán)處刻蝕通孔,進(jìn)行薄膜多層電路的制作。這種技術(shù)的突出優(yōu)點(diǎn)是所有芯片或無(wú)源器件(如耦合器、濾波器等)可以同時(shí)裝配,裝配不采用金絲鍵合手段也不用倒裝芯片,以解決毫米波頻段金絲鍵合帶來(lái)的一致性控制以及寄生效應(yīng)難題;同時(shí)也可解決采用倒裝芯片帶來(lái)的功率耗散問(wèn)題,芯片的熱量可以通過(guò)金屬底板快速散去。
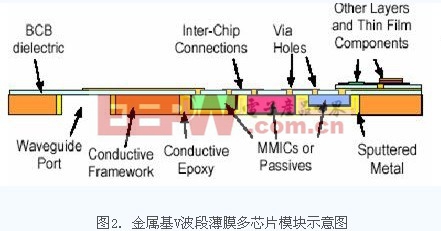
3.3 A l/SiC復(fù)合材料基板上HDI技術(shù)T/R組件
1997年,Lockheed Martin 公司報(bào)道了和GE 公司合作開(kāi)發(fā)的基于Al/SiC材料基板的薄膜多層電路的T/R組件(7),結(jié)構(gòu)圖如圖3所示。采用Al/SiC材料做T/R組件的基板,主要考慮該材料不僅導(dǎo)熱率較高(接近氮化鋁,約160W/moK),而且熱張系數(shù)與GaAs或Si有源芯片接近,有利于直接貼裝芯片。此外該材料密度低,有利于降低組件重量。 采用Al/SiC材料作基板,必須預(yù)先加工成形并進(jìn)行鍍Ni/Au金屬化,有源芯片和無(wú)源器件可以直接貼裝于凹腔內(nèi),并使其與基板表面在同一平面上,其中高功率GaAs芯片采用 AuSn高溫焊料焊于基板凹腔內(nèi),以保證熱傳導(dǎo)并降低器件結(jié)點(diǎn)溫度;非功率芯片和無(wú)源器件可以采用導(dǎo)電膠貼于基板凹腔內(nèi)。然后在其上實(shí)施HDI技術(shù)(薄膜高密度多層互連),即采用膠粘劑復(fù)合一層聚酰亞胺膜(kapton), 用激光在對(duì)應(yīng)芯片焊盤(pán)以及基板上需要的位置開(kāi)孔,在孔及基板上采用濺射工藝實(shí)現(xiàn)金屬化(Ti/Cu/Ti),然后采用激光或光刻的方法刻出圖形及帶線。以此類(lèi)推,實(shí)現(xiàn)多層。
DIY機(jī)械鍵盤(pán)相關(guān)社區(qū):機(jī)械鍵盤(pán)DIY
評(píng)論