基于電芯替換的電動汽車動力電池組維護方法
鋰電池憑借其能量密度高、體積密度高、工作電壓高、無記憶效應(yīng)、自放電低且無污染等優(yōu)點,成為電動汽車動力源的最佳選擇。為滿足電動汽車功率驅(qū)動需求,一般需要將鋰電池電芯串聯(lián)使用以提高電壓等級。
本文引用地址:http://www.ex-cimer.com/article/201808/386104.htm串聯(lián)電池組存在循環(huán)使用壽命達不到設(shè)計壽命的問題,一方面是在串聯(lián)電池組的實際應(yīng)用中,個別電芯的衰減速率明顯快于其他電芯,從而影響該電芯所在電池組的性能;另一方面是各電芯的充/放電特性不一致,電芯的充/放電特性差異會造成充/放電時電量的不平衡,從而對過充電或過放電的電池造成損害,影響整個電池組的使用壽命。
運營數(shù)據(jù)表明,采用傳統(tǒng)充電方式,鋰電池組(80V 60Ah磷酸鐵鋰電池組)充/放電近500多次循環(huán)后,實際可用容量降為原來的80%左右,而且隨著充電次數(shù)的增加,實際可用容量還將進一步下降。
顯然,如何維持動力電池組的可用容量和延長使用壽命是目前急需解決的重要問題。此外,某些電池組在使用過程中循環(huán)壽命嚴重低于正常值。以下分析某電動汽車動力電池組可用容量驟然下降的現(xiàn)象,指出“短板電芯”是導(dǎo)致可用容量下降的原因之一,提出用電芯替換方法來提高串聯(lián)電芯的一致性水平。
試驗結(jié)果表明使用該方法可使某性能異常的磷酸鐵鋰電池組(80V 60Ah)實測循環(huán)壽命從158次提高至629次,提高了成組動力電池組的實際可用容量和循環(huán)使用壽命。
1.某動力電池組循環(huán)壽命測試分析
1.1 動力電池組循環(huán)壽命測試方案
動力電池組主要由24節(jié)磷酸鐵鋰電池電芯、電池管理系統(tǒng)以及電連接器等組成。每節(jié)磷酸鐵鋰電芯參數(shù)為3.2V60Ah。
使用循環(huán)充放電測試儀對動力電池組進行循環(huán)壽命測試,試驗方法和步驟如下:
(1)20℃下靜置10min,以87.6V電壓30A電流恒流充電,然后恒壓充電至電流為3A時,充電停止;保護電壓3.7V,當電芯電壓超過3.7V時充電立即停止;
(2)靜置10min,5A電流恒流放電至2.8V;
(3)重復(fù)步驟(1)-(2),循環(huán)至初始容量的80%左右,統(tǒng)計循環(huán)壽命。
記錄的過程數(shù)據(jù)包含:時間、端電壓、電流、溫度、充放電容量、壓差、24 節(jié)電芯各自的電壓。
1.2 動力電池組循環(huán)壽命測試結(jié)果
電池的循環(huán)使用壽命是評價電池性能的一項重要指標,指以電池充電和放電1次為1個循環(huán),按照一定測試標準,當電池容量(一般為放電容量)降到某一規(guī)定值(一般規(guī)定為初始容量的80%)以前,電池經(jīng)歷的充/放電循環(huán)總次數(shù)。
根據(jù)以上測試方案,電池組的初始容量為60Ah,當電池組循環(huán)過程中低于48Ah時,停止測試,統(tǒng)計循環(huán)次數(shù)為159次。
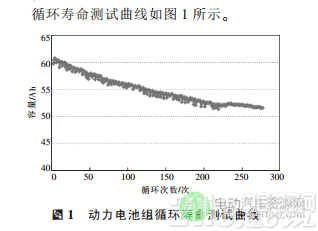
循環(huán)壽命測試曲線如圖1所示。電動汽車動力電池組循環(huán)壽命159次后,放電容量已經(jīng)下降到47.9Ah,首次跌破48Ah(初始容量的80%),所以此動力電池組的循環(huán)壽命為158次,此循環(huán)壽命遠低于平均次數(shù),判斷此電池組為異常電池組。
2.動力電池組循環(huán)壽命短板效應(yīng)分析
2.1 短板效應(yīng)
短板效應(yīng)又稱木桶原理,即一個水桶無論有多高,它盛水的高度取決于其中最短的那塊木板,要想提高木桶的容量,就應(yīng)該設(shè)法加高最短的那塊木板的高度,這是最有效也是惟一的途徑。該原理形象地描述了怎樣確定一個整體的實力以及怎樣提高整體實力的問題,已廣泛應(yīng)用在企業(yè)管理、人力資源和經(jīng)濟管理等方面。
在串聯(lián)電池組的實際應(yīng)用中,由于電芯的不一致性,為了保證電芯不過充或過放,對每個電芯設(shè)置了統(tǒng)一的充電及放電保護電壓。所以當某個電芯電壓達到了保護電壓時,動力電池組即停止充電或放電過程。
2.2 動力電池組循環(huán)壽命衰減研究
動力電池組循環(huán)充/放電過程中,對之前159次充電過程中最早達到充電保護上限電壓的電芯進行統(tǒng)計,統(tǒng)計結(jié)果如圖2所示。
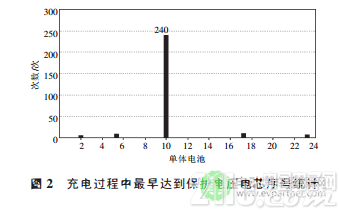
動力電池組在做循環(huán)壽命測試中,24節(jié)電芯中的第2,5,10,17,23節(jié)到達充電保護上限電壓的次數(shù)分別為7,10,240,11,8次,第10節(jié)到達充電保護上限電壓的次數(shù)占總次數(shù)的86.16%。
根據(jù)“短板效應(yīng)”分析,24節(jié)電芯中的第10節(jié)是電動汽車動力電池組循環(huán)壽命縮短的主要原因,將這樣的電芯稱為“短板電芯”。通過更換“短板電芯”,提高電芯一致性,有望提升動力電池組的可用容量。
3.電芯替換技術(shù)
電芯替換技術(shù)主要解決電池組在電芯替換時,替換的電芯與原電池組的匹配問題,匹配性的好壞直接決定了替換后電池組的使用壽命。
3.1 電池配組系統(tǒng)
電池配組系統(tǒng)的工作流程如下:
(1)用于替換的電芯(可以是新電芯也可以是舊電芯),通過電芯性能測試系統(tǒng),獲得該電池的開路電壓、容量、充/放電曲線等信息,并錄入到電芯模型庫中,該模型庫中存有所有擬用于替換的電芯信息;
(2)待配組的電池組通過電池組性能檢測系統(tǒng),獲得電池組內(nèi)所有電芯的開路電壓、容量、充/放電曲線等信息,準確挑出需要更換的“短板電芯”,同時根據(jù)該箱電池中其他電芯的真實性能和容量整體評估的結(jié)果,給出需要進行匹配的電芯需求信息;
(3)通過電芯的開路電壓、容量、充/放電曲線的比對,在電芯模型庫中,找出匹配度較好的電芯,測試通過則替換過程完成。
3.2 電池組性能檢測
電池組性能檢測系統(tǒng)主要是有2個功能:通過對電池組內(nèi)所有電芯的開路電壓、容量、充/放電曲線等信息查詢,準確挑出需要更換的“短板電芯”;驗證重新裝配后的電池組是否匹配良好。
檢測系統(tǒng)構(gòu)成的便捷式設(shè)備主要由程控充電機、程控負載、無線采集系統(tǒng)、總控制器組成。電池組性能檢測設(shè)備原理如圖3所示。系統(tǒng)通過對電池組中BMS(電池管理系統(tǒng))的通信獲得電芯信息。
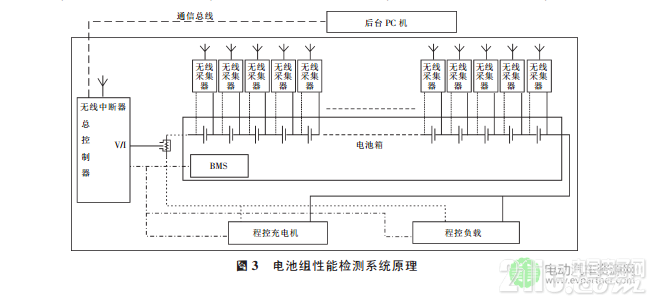
以替換前后動力電池組為例,電池組性能檢測系統(tǒng)開啟,對電池組各單體電芯到達放電截止電壓點時(截止電壓2.8V)電壓、壓差(放電截止時單體電壓最高值和最低值差)、充/放電容量等信息進行檢測。替換前電池組放電截止時所有單體電芯的電壓信息見表1。
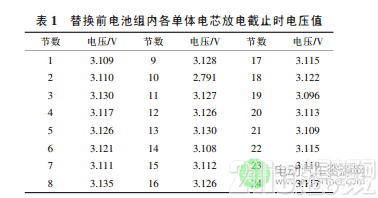
檢測數(shù)據(jù)表明,第10節(jié)電芯的充電容量為51.54Ah,放電容量為52.34Ah,初始放電容量為60Ah,充/放電值均比整組低,放電時尤為明顯,放電值略低0.05V左右,說明充電和放電容量都不足,此時整組電池容量為初始容量的87.23%,第10節(jié)單體放電時最先到達放電截止電壓,且壓差為0.344V,不符合壓差不超過0.22V的規(guī)定,故第10節(jié)電芯屬于短板電芯,此時的電池組需要維護。
將第10節(jié)電芯替換后,電池組放電截止時所有單體電芯的電壓信息見表2。替換后電池組容量57.58Ah,壓差0.213V?;谏鲜鲅芯刻岢鎏鎿Q指標,即電池容量下降為初始容量的90%~92%,壓差達到0.22V左右時,要對電池進行維護,參考值以容量值為主、壓差值為輔。
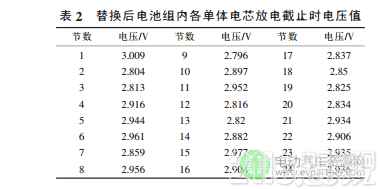
4.電芯替換后循環(huán)壽命試驗驗
證重組匹配成功后,按照測試方案繼續(xù)進行測試,結(jié)果如圖4所示。
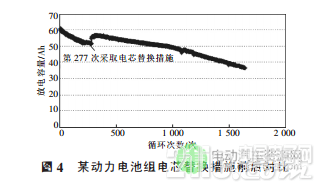
在電芯替換前,針對某一電池組的循環(huán)測試過程中,因其容量衰減速率較快,在其循環(huán)到277次,容量降至52.34Ah(約為初始容量的87%)。對其采用電芯替換措施后,其放電容量立刻得到提升,當循環(huán)次數(shù)為1062次,放電容量為47.99Ah(約為初始容量的80%),表明電池組循環(huán)壽命為1061次,說明電芯替換方法能有效延長電池組壽命。
5.結(jié)語
電芯替換技術(shù)可以提高電芯的一致性,保持電池組的可用容量和延長循環(huán)使用壽命。尤其在部分電池組中存在“短板電芯”導(dǎo)致可用容量驟降及壽命縮短的情況下,維護效果更加顯著。隨著電動汽車的推廣,基于電芯替換的電動汽車動力電池組維護技術(shù),具有良好的經(jīng)濟性和廣闊的應(yīng)用前景。
評論