新型電路板技術(shù)滿足數(shù)字電源的需求(1)
在本應(yīng)用中,重量和尺寸都至關(guān)重要,兩者一旦增加就會(huì)直接影響到車輛的可行駛里程數(shù)。為了減輕重量并縮小尺寸,本實(shí)例中的電池組正前部安裝了一個(gè)由控制邏輯單元和8塊DirectFET功率器件組成的電機(jī)控制器。經(jīng)驗(yàn)證,該DWPCB解決方案在整合控制邏輯單元和功率單元方面的效果非常理想,且將PCB數(shù)量由兩塊縮減至一塊,并省去了相關(guān)的接頭和布線。
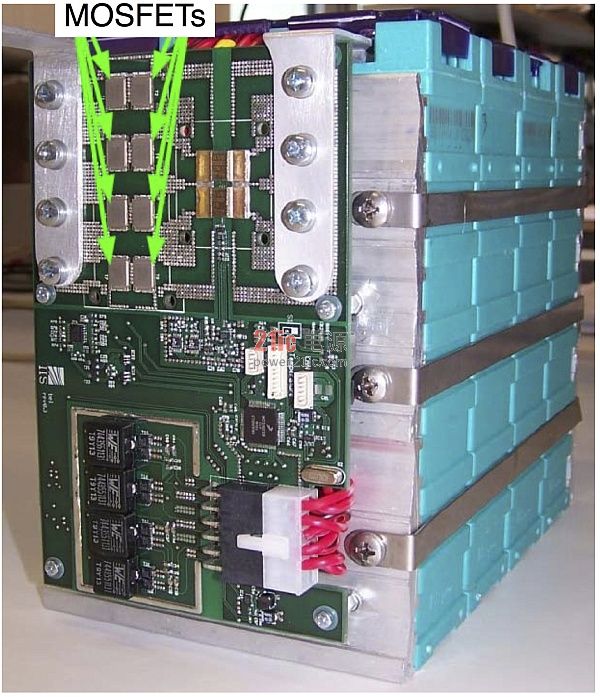
圖5:輕型電動(dòng)車的鋰離子電池組/電機(jī)控制器裝置。
設(shè)計(jì)過(guò)程中面臨的挑戰(zhàn)在于要將100A/300A的電流發(fā)送至一個(gè)FR-4電路板,再到DirectFET,最終傳遞到總線上。對(duì)此,Häusermann公司開(kāi)發(fā)的多功能DWPCB技術(shù)為設(shè)計(jì)人員提供了多種選擇:從單層功率分配到帶有一體化熱通孔和散熱面的多層設(shè)計(jì)。
圖6為我們展示了一種性價(jià)比最高的設(shè)計(jì)方案。
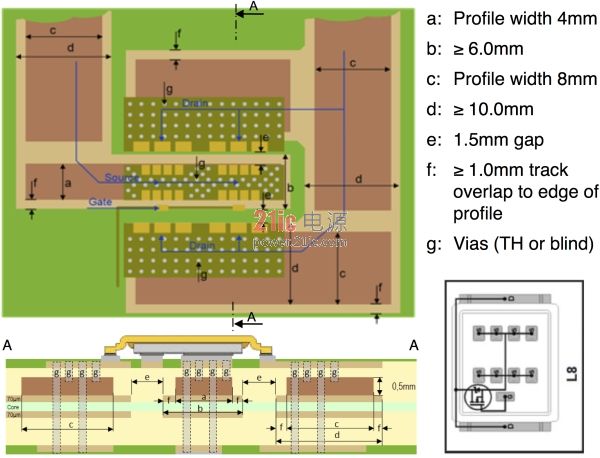
圖6:使用HSMTec的DirectFET封裝的MiB布局。
在該方案中,型材焊接在一個(gè)由高耐熱性(Tg)且敷銅2盎司(70μ)的FR-4覆層組成的內(nèi)芯中。由于所有的型材都位于相同的基準(zhǔn)面上,焊接器件的安裝和運(yùn)行時(shí)間得以優(yōu)化,而且與型材安裝于多個(gè)不同層的設(shè)計(jì)方案相比,后續(xù)大規(guī)模分層過(guò)程中的嵌入任務(wù)會(huì)更加簡(jiǎn)單。
嵌入型材同時(shí)可為電路板表面提供更多空間:用于高電流路徑的空間僅限于導(dǎo)孔陣列,用以使電流通過(guò)嵌入型材。同時(shí),支撐型材的寬路徑僅限于內(nèi)層之中。
大功率微孔
電流通過(guò)激光微孔到達(dá)高電流型材,該技術(shù)普遍運(yùn)用于多種MiB中。盡管激光孔的直徑一般為100μ或更小,但MiB應(yīng)用中最重要的是導(dǎo)電元件的長(zhǎng)度(在該實(shí)例中為微孔深度)和用于電流傳輸?shù)你~的橫截面面積。
銅橫截面面積有若干種計(jì)算方法。公式(2)中使用鉆孔圓周直徑和內(nèi)鍍圓周直徑算出的表面積的不同得出銅橫截面面積。由此可得出微孔陣列的熱阻率:
Rθ array = l/k × (Nvias × {π×[(D1/2)2 - (D2/2)2]}) (2)
式中:
I—微孔深度;
k—銅的導(dǎo)電率(約380W/m-K);
D1—鉆孔圓周直徑;
D2—成品(內(nèi)鍍)孔圓周直徑;
Nvias—陣列中微孔個(gè)數(shù)。
另外,由于激光微孔很小且鉆孔的有效命中率為每分鐘10,000次以上(CO2銅箔直接加工工藝),很多激光微孔均可有效打通于隔熱盤上,且成本較低。一塊含有1296個(gè)微孔的100mm2的隔熱盤的熱阻率可高達(dá)約0.01W/℃:相當(dāng)于使用釬焊接頭將器件的散熱片焊接在隔熱盤上。
除了用于使電流通過(guò)埋放型材的微孔,本設(shè)計(jì)方案中還通過(guò)底層散熱面上的熱通孔擴(kuò)大了器件的散熱區(qū)域。其中所面臨的制備挑戰(zhàn)包括如何在銅金屬主體上實(shí)現(xiàn)打孔進(jìn)刀量少于FR-4打孔進(jìn)刀量的三分之一。
然而,熱通孔一般來(lái)說(shuō)就是熱導(dǎo)管,所以本設(shè)計(jì)方案中層3焊點(diǎn)中出現(xiàn)的釘頭并不會(huì)影響到電性能。本設(shè)計(jì)方案旨在得到一個(gè)干凈清潔的孔并使銅均勻地沉積,進(jìn)而提升熱能傳輸能力。熱通孔陣列可以有效地使熱能向下通過(guò)電路板傳輸至背端散熱面:一個(gè)普通的微孔陣列的傳導(dǎo)率在20W/m-K~30W/m-K之間,是FR-4傳導(dǎo)率的100多倍。
對(duì)電路板內(nèi)部功率路徑的有效管理可以為外層提供信號(hào)和控制布線的空間,同時(shí),并行FET的門信號(hào)也位于電路板表面。圖6展示了這類電路板的典型布局以及型材在蝕刻核心載流路徑上的分布情況。
為清晰起見(jiàn),型材之間的空隙被拉大:空隙體積會(huì)使總導(dǎo)體體積發(fā)生小于0.1%的變化。圖7展示了本設(shè)計(jì)最終呈現(xiàn)的清晰布局。
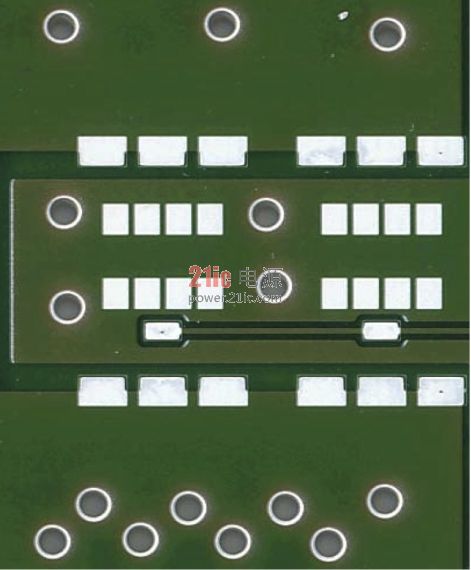
圖7:成品電路板:DirectFET焊盤。
MiB = 電路板的價(jià)值
面對(duì)這樣一個(gè)簡(jiǎn)單的創(chuàng)新型解決方案,人們通常問(wèn)的第一個(gè)問(wèn)題便是:得花多少錢?
用到該解決方案首先考慮的是可靠性和性能(電動(dòng)汽車壽命為15年~25年,功能密度的改善意味著質(zhì)量和體積的減少和運(yùn)行自主性的增加),成本公式為零和,即替代技術(shù)要么與原有技術(shù)等同且取代原有技術(shù)后會(huì)遵循相同的成本下降曲線,要么該替代技術(shù)可以在成本、性能、可靠性或以上三個(gè)方面同時(shí)帶來(lái)數(shù)量級(jí)的改善效果。成本下降曲線取決于一套潛在的數(shù)學(xué)關(guān)系,這在BPA即將出版的關(guān)于學(xué)習(xí)曲線理論和對(duì)MiB技術(shù)相關(guān)影響的文章中會(huì)有進(jìn)一步的探討。
以上設(shè)計(jì)實(shí)例基本上實(shí)現(xiàn)了兩個(gè)目標(biāo):
● 應(yīng)用了最新的等量功率器件,使熱能和電流管理所需的電路板空間減少了30%。
● 通過(guò)降低功率板面積、除去控制子板、用更小的鰭片組和底盤螺柱代替PIH(銷釘孔)TO器件所需的垂直散熱片以及使用直連電源總線的方式代替高電流布線來(lái)減小電路板的體積和重量。
與最初的設(shè)計(jì)方案相比,MiB解決方案僅在組件數(shù)目和組裝成本方面就節(jié)省了約13%。完整的成本/功能分析需考慮到重量和體積的減少所帶來(lái)的利潤(rùn),這也是下一步研究的課題。
本設(shè)計(jì)結(jié)果已成為一項(xiàng)印刷電路解決方案,用以應(yīng)對(duì)尤其是使用最新SMT封裝的中等功率應(yīng)用的散熱和功率分配方面的挑戰(zhàn)。這些器件的表面貼裝特性意味著電路板必須能夠提供低電阻熱能和電氣路徑。該設(shè)計(jì)是將傳統(tǒng)印刷電路技術(shù)(包括激光和機(jī)械鉆孔)與新型技術(shù)相結(jié)合用以面對(duì)數(shù)字電源挑戰(zhàn)的最佳示例。
評(píng)論