OLED發(fā)光原理、結(jié)構(gòu)及關(guān)鍵技術(shù)深度圖文解析
深度解析OLED結(jié)構(gòu)及發(fā)光原理關(guān)鍵技術(shù)。OLED的原文是Organic Light Emitting Diode,中文意思就是“有機(jī)發(fā)光顯示技術(shù)”。其原理是在兩電極之間夾上有機(jī)發(fā)光層,當(dāng)正負(fù)極電子在此有機(jī)材料中相遇時(shí)就會(huì)發(fā)光,其組件結(jié)構(gòu)比目前流行的TFT LCD簡(jiǎn)單,生產(chǎn)成本只有TFT LCD的三到四成左右。除了生產(chǎn)成本便宜之外,OLED還有許多優(yōu)勢(shì),比如自身發(fā)光的特性,目前LCD都需要背光模塊(在液晶后面加燈管),但OLED通電之后就會(huì)自己發(fā)光,可以省掉燈管的重量體積及耗電量(燈管耗電量幾乎占整個(gè)液晶屏幕的一半),不僅讓產(chǎn)品厚度只剩兩厘米左右,操作電壓更低到2至10伏特,加上OLED的反應(yīng)時(shí)間(小于10ms)及色彩都比TFT LCD出色,更有可彎曲的特性,讓它的應(yīng)用范圍極廣。
本文引用地址:http://www.ex-cimer.com/article/201808/391418.htmOLED結(jié)構(gòu)及發(fā)光原理
OLED的基本結(jié)構(gòu)是在銦錫氧化物(ITO)玻璃上制作一層幾十納米厚的有機(jī)發(fā)光材料作發(fā)光層,發(fā)光層上方有一層低功函數(shù)的金屬電極,構(gòu)成如三明治的結(jié)構(gòu)。
OLED的基本結(jié)構(gòu)主要包括:
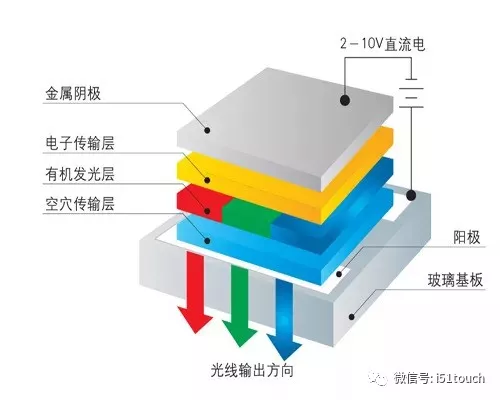
基板(透明塑料、玻璃、金屬箔)——基層用來(lái)支撐整個(gè)OLED。
陽(yáng)極(透明)——陽(yáng)極在電流流過(guò)設(shè)備時(shí)消除電子(增加電子“空穴”)。
空穴傳輸層——該層由有機(jī)材料分子構(gòu)成,這些分子傳輸由陽(yáng)極而來(lái)的“空穴”。
發(fā)光層——該層由有機(jī)材料分子(不同于導(dǎo)電層)構(gòu)成,發(fā)光過(guò)程在這一層進(jìn)行。
電子傳輸層——該層由有機(jī)材料分子構(gòu)成,這些分子傳輸由陰極而來(lái)的“電子”。
陰極(可以是透明的,也可以不透明,視OLED類(lèi)型而定)——當(dāng)設(shè)備內(nèi)有電流流通時(shí),陰極會(huì)將電子注入電路。
OLED是雙注入型發(fā)光器件,在外界電壓的驅(qū)動(dòng)下,由電極注入的電子和空穴在發(fā)光層中復(fù)合形成處于束縛能級(jí)的電子空穴對(duì)即激子,激子輻射退激發(fā)發(fā)出光子,產(chǎn)生可見(jiàn)光。為增強(qiáng)電子和空穴的注入和傳輸能力,通常在ITO與發(fā)光層之間增加一層空穴傳輸層,在發(fā)光層與金屬電極之間增加一層電子傳輸層,從而提高發(fā)光性能。其中,空穴由陽(yáng)極注入,電子由陰極注入??昭ㄔ谟袡C(jī)材料的最高占據(jù)分子軌道(HOMO)上跳躍傳輸,電子在有機(jī)材料的最低未占據(jù)分子軌道(LUMO)上跳躍傳輸。
OLED的發(fā)光過(guò)程通常有以下5個(gè)基本階段:
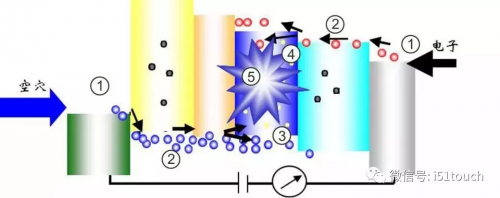
載流子注入:在外加電場(chǎng)作用下,電子和空穴分別從陰極和陽(yáng)極向夾在電極之間的有機(jī)功能層注入。
載流子傳輸:注入的電子和空穴分別從電子傳輸層和空穴傳輸層向發(fā)光層遷移。
載流子復(fù)合:電子和空穴注入到發(fā)光層后,由于庫(kù)倫力的作用束縛在一起形成電子空穴對(duì),即激子。
激子遷移:由于電子和空穴傳輸?shù)牟黄胶?,激子的主要形成區(qū)域通常不會(huì)覆蓋整個(gè)發(fā)光層,因而會(huì)由于濃度梯度產(chǎn)生擴(kuò)散遷移。
激子輻射退激發(fā)出光子:激子輻射躍遷,發(fā)出光子,釋放能量。
OLED發(fā)光的顏色取決于發(fā)光層有機(jī)分子的類(lèi)型,在同一片OLED上放置幾種有機(jī)薄膜,就構(gòu)成彩色顯示器。光的亮度或強(qiáng)度取決于發(fā)光材料的性能以及施加電流的大小,對(duì)同一OLED,電流越大,光的亮度就越高。
OLED的制造原理
OLED組件系由n型有機(jī)材料、p型有機(jī)材料、陰極金屬及陽(yáng)極金屬所構(gòu)成。電子(空穴)由陰極(陽(yáng)極)注入,經(jīng)過(guò)n型(p型)有機(jī)材料傳導(dǎo)至發(fā)光層(一般為n型材料),經(jīng)由再結(jié)合而放光。一般而言,OLED元件制作的玻璃基板上先濺鍍ITO作為陽(yáng)極,再以真空熱蒸鍍之方式,依序鍍上p型和n型有機(jī)材料,及低功函數(shù)之金屬陰極。由于有機(jī)材料易與水氣或氧氣作用,產(chǎn)生暗點(diǎn)(Dark spot)而使元件不發(fā)亮。因此此元件于真空鍍膜完畢后,必須于無(wú)水氣及氧氣之環(huán)境下進(jìn)行封裝工藝。

在陰極金屬與陽(yáng)極ITO之間,目前廣為應(yīng)用的元件結(jié)構(gòu)一般而言可分為5層。如圖所示,從靠近ITO側(cè)依序?yàn)椋嚎昭ㄗ⑷雽?、空穴傳輸層、發(fā)光層、電子傳輸層、電子注入層。
而至于電子傳輸層,系為n型之有機(jī)材料,其特性為具有較高之電子遷移率,當(dāng)電子由電子傳輸層至空穴電子傳輸層介面時(shí),由于電子傳輸層之最低非占據(jù)分子軌域較空穴傳輸層之LUMO高出甚多,電子不易跨越此一能障進(jìn)入空穴傳輸層,遂被阻擋于此介面。此時(shí)空穴由空穴傳輸層傳至介面附近與電子再結(jié)合而產(chǎn)生激子(Exciton),而Exciton會(huì)以放光及非放光之形式進(jìn)行能量釋放。以一般螢光材料系統(tǒng)而言,由選擇率之計(jì)算僅得25%之電子空穴對(duì)系以放光之形式做再結(jié)合,其余75%之能量則以放熱之形式散逸。近年來(lái),正積極被開(kāi)發(fā)磷光材料成為新一代的OLED材料,此類(lèi)材料可打破選擇率之限制,以提高內(nèi)部量子效率至接近100%。
在兩層元件中,n型有機(jī)材料-即電子傳輸層-亦同時(shí)被當(dāng)作發(fā)光層,其發(fā)光波長(zhǎng)系由HOMO及LUMO之能量差所決定。然而,好的電子傳輸層-即電子遷移率高之材料-并不一定為放光效率佳之材料,因此目前一般之做法,系將高螢光度的有機(jī)色料,摻雜(Doped)于電子傳輸層中靠近空穴傳輸層之部分,又稱(chēng)為發(fā)光層,其體積比約為1%至3%。摻雜技術(shù)開(kāi)發(fā)系用于增強(qiáng)原材料之螢光量子吸收率的重點(diǎn)技術(shù),一般所選擇的材料為螢光量子吸收率高的染料。
陰極之金屬材料,傳統(tǒng)上系使用低功函數(shù)之金屬材料(或合金),如鎂合金,以利電子由陰極注入至電子傳輸層,此外一種普遍之做法,系導(dǎo)入一層電子注入層,其構(gòu)成為一極薄之低功函數(shù)金屬鹵化物或氧化物,如LiF或Li2O,此可大幅降低陰極與電子傳輸層之能障,降低驅(qū)動(dòng)電壓。
由于空穴傳輸層材料之HOMO值與ITO仍有差距,此外ITO陽(yáng)極在長(zhǎng)時(shí)間操作后,有可能釋放出氧氣,并破壞有機(jī)層產(chǎn)生暗點(diǎn)。故在ITO及空穴傳輸層之間,插入一空穴注入層,其HOMO值恰介于ITO及空穴傳輸層之間,有利于空穴注入OLED元件,且其薄膜之特性可阻隔ITO中之氧氣進(jìn)入OLED元件,以延長(zhǎng)元件壽命。
OLED的制備工藝
OLED因其構(gòu)造簡(jiǎn)單,所以生產(chǎn)流程不像LCD制造程序那樣繁復(fù)。但由于現(xiàn)今OLED制程設(shè)備還在不斷改良階段,并沒(méi)有統(tǒng)一標(biāo)準(zhǔn)的量產(chǎn)技術(shù),而主動(dòng)與被動(dòng)驅(qū)動(dòng)以及全彩化方法的不同都會(huì)影響OLED的制程和機(jī)組的設(shè)計(jì)。但是,整個(gè)生產(chǎn)過(guò)程需要潔凈的環(huán)境和配套的工藝和設(shè)備。改善器件的性能不僅要從構(gòu)成器件的基礎(chǔ),即材料的化學(xué)結(jié)構(gòu)入手,提高材料性能和豐富材料的種類(lèi);還要深入了解器件的物理過(guò)程和內(nèi)部的物理機(jī)制,有針對(duì)性地改進(jìn)器件的結(jié)構(gòu)以提高器件的性能。兩者相輔相成,不斷推進(jìn)OLED技術(shù)的發(fā)展。
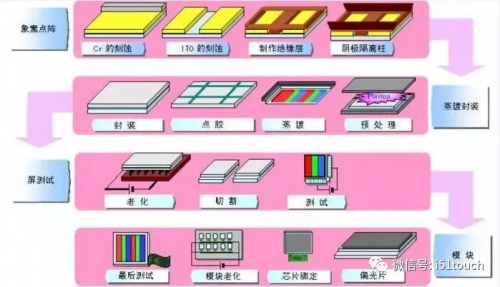
ITO基板預(yù)處理工藝
首先需要準(zhǔn)備導(dǎo)電性能好和透射率高的導(dǎo)電玻璃,通常使用ITO玻璃。高性能的ITO玻璃加工工藝比較復(fù)雜,市面上可以直接買(mǎi)到。ITO作為電極,需要特定的形狀、尺寸和圖案來(lái)滿足器件設(shè)計(jì)的要求,可委托廠家按要求進(jìn)行切割和通過(guò)光刻形成圖案,也可在實(shí)驗(yàn)室自己進(jìn)行ITO玻璃的刻蝕,得到所需的基片和電極圖形?;砻娴钠秸取⑶鍧嵍榷紩?huì)影響有機(jī)薄膜材料的生長(zhǎng)情況和OLED性能,必須對(duì)ITO表面進(jìn)行嚴(yán)格清洗。
常用的ITO薄膜表面預(yù)處理方法為:化學(xué)方法(酸堿處理)和物理方法(O2等離子體處理、惰性氣體濺射)。
酸堿處理
固體表面的結(jié)構(gòu)和組成都與內(nèi)部不同,處于表面的原子或離子表現(xiàn)為配位上的不飽和性,這是由于形成固體表面時(shí)被切斷的化學(xué)鍵造成的。
正是由于這一原因,固體表面極易吸附外來(lái)原子,使表面產(chǎn)生污染。因環(huán)境空氣中存在大量水份,所以水是固體表面最常見(jiàn)的污染物。
由于金屬氧化物表面被切斷的化學(xué)鍵為離子鍵或強(qiáng)極性鍵,易與極性很強(qiáng)的水分子結(jié)合,因此,絕大多數(shù)金屬氧化物的清潔表面,都是被水吸附污染了的。
在多數(shù)情況下,水在金屬氧化物表面最終解離吸附生成OH-及H+,其吸附中心分別為表面金屬離子以及氧離子。
根據(jù)酸堿理論,M+是酸中心,O-是堿中心,此時(shí)水解離吸附是在一對(duì)酸堿中心進(jìn)行的。
在對(duì)ITO表面的水進(jìn)行解離之后,再使用酸堿處理ITO金屬氧化物表面時(shí),酸中的H+、堿中的OH-分別被堿中心和酸中心吸附,形成一層偶極層,因而改變了ITO表面的功函數(shù)。
等離子體處理
等離子體的作用通常是改變表面粗糙度和提高功函數(shù)。研究發(fā)現(xiàn),等離子作用對(duì)表面粗糙度的影響不大,只能使ITO的均方根粗糙度從1.8nm降到1.6nm,但對(duì)功函數(shù)的影響卻較大。用等離子體處理提高功函數(shù)的方法也不盡相同。
氧等離子處理是通過(guò)補(bǔ)充ITO表面的氧空位來(lái)提高表面氧含量的。
操作方法為:將ITO基片依次在清洗液、去離子水、乙醇和丙酮的混合液、去離子水超聲清洗以除去基片表面物理吸附和化學(xué)吸附的污染物,然后將清洗干凈的基片放到潔凈工作臺(tái)內(nèi),烘烤或者用高速噴出的氮?dú)獯蹈蒊TO表面,最后對(duì)ITO表面進(jìn)行氧等離子體轟擊或者紫外臭氧處理。ITO玻璃的預(yù)處理有利于除去ITO表面可能的污染物,提高ITO表面的功函數(shù),減小ITO電極到有機(jī)功能材料的空穴注入勢(shì)壘。
成膜技術(shù)
制備OLED材料包括有機(jī)小分子、高分子聚合物、金屬及合金等。大部分有機(jī)小分子薄膜通過(guò)真空熱蒸鍍來(lái)制備,可溶性有機(jī)小分子和聚合物薄膜可通過(guò)更為簡(jiǎn)單、快速和低成本的溶液法制備,先后開(kāi)發(fā)出了旋涂法、噴涂法、絲網(wǎng)印刷、激光轉(zhuǎn)印等技術(shù)。金屬及合金薄膜通常采用真空熱蒸鍍來(lái)制備,為了實(shí)現(xiàn)全溶液法制備OLED,也開(kāi)發(fā)了基于液態(tài)金屬如導(dǎo)電銀漿刷涂的溶液制備方法。
評(píng)論