SiC 功率器件中的溝槽結(jié)構(gòu)測量
汽車和清潔能源領(lǐng)域的制造商需要更高效的功率器件,能夠適應(yīng)更高的電壓,擁有更快的開關(guān)速度,并且比傳統(tǒng)硅基功率器件提供更低的損耗,而溝槽結(jié)構(gòu)的 SiC 功率器件可以實現(xiàn)這一點。
本文引用地址:http://www.ex-cimer.com/article/202406/459969.htm但是,雖然基于溝槽的架構(gòu)可以降低導(dǎo)通電阻并提高載流子遷移率,但它們也帶來了更高的復(fù)雜性。對于 SiC 功率器件制造商來說,準確測量外延層生長和這些溝槽中注入層深度的能力是相當重要的,特別是在面臨不斷增加的制造復(fù)雜性時。
今天我們分享一下來自O(shè)nto Innovation 應(yīng)用開發(fā)總監(jiān)Nick Keller的文章,來重點介紹下SiC 功率器件中的溝槽結(jié)構(gòu)測量:
光學(xué)臨界尺寸 (OCD) 計量系統(tǒng)
來測量溝槽深度以及底部和頂部臨界尺寸 (CD)
隱形挑戰(zhàn)
使用基于溝槽的架構(gòu)測量 SiC 功率器件時的核心挑戰(zhàn)是:自上而下的測量方法無法看到凹入式結(jié)構(gòu)和垂直凹入式結(jié)構(gòu)。這適用于臨界尺寸掃描電子顯微鏡 (CD-SEM) 和基于圖像的顯微鏡等方法。因此,制造商已轉(zhuǎn)向 OCD 進行尺寸計量。OCD 提供耗時不到一秒的無損測量,具有埃級重復(fù)性的高精度,并且是一種數(shù)據(jù)豐富的計量技術(shù),能夠在復(fù)雜的 3D 結(jié)構(gòu)中同時測量數(shù)十個參數(shù)。
對于專為功率器件市場設(shè)計的 OCD 系統(tǒng),制造商經(jīng)常使用光譜橢偏儀 (SE)(薄膜測量的黃金標準)和偏振光譜反射儀 (SR)。SE 用于收集斜入射時 2D 和 3D 周期性結(jié)構(gòu)的深紫外 (DUV) 到近紅外 (NIR) 范圍內(nèi)的鏡面反射率,而對于 SR,除了法向入射外,其他情況相同。
這樣做有一個缺點:作為一種間接方法,OCD 需要一個模型來解釋復(fù)雜的光譜數(shù)據(jù)。因此,OCD 計量可能不準確,并且設(shè)置時間較長。但是,好消息是:模型引導(dǎo)機器學(xué)習(xí) (MGML) 算法可以提高準確性并縮短解決時間。
在我們的研究中,我們使用 SE 和 SR 測量 SiC 功率器件中的這些基于溝槽的結(jié)構(gòu),然后使用基于 RCWA 的 EM 求解器分析數(shù)據(jù)。然后,該信息用于運行高級過程控制。
雖然 OCD 可用于 SiC 溝槽 MOSFET 工藝流程中的多個工藝步驟,但溝槽蝕刻后的測量尤其令人感興趣。溝槽蝕刻是關(guān)鍵,因為底部寬度、底部圓角、側(cè)壁角度、深度和側(cè)壁粗糙度有助于關(guān)鍵性能屬性,包括擊穿電壓、導(dǎo)通電阻、溝道遷移率和時間相關(guān)的柵極氧化物擊穿。
SiC蝕刻具有挑戰(zhàn)性,因為它是一種極其堅硬的物質(zhì),化學(xué)性質(zhì)穩(wěn)定,并且對SiO 2硬掩模的選擇性較低。
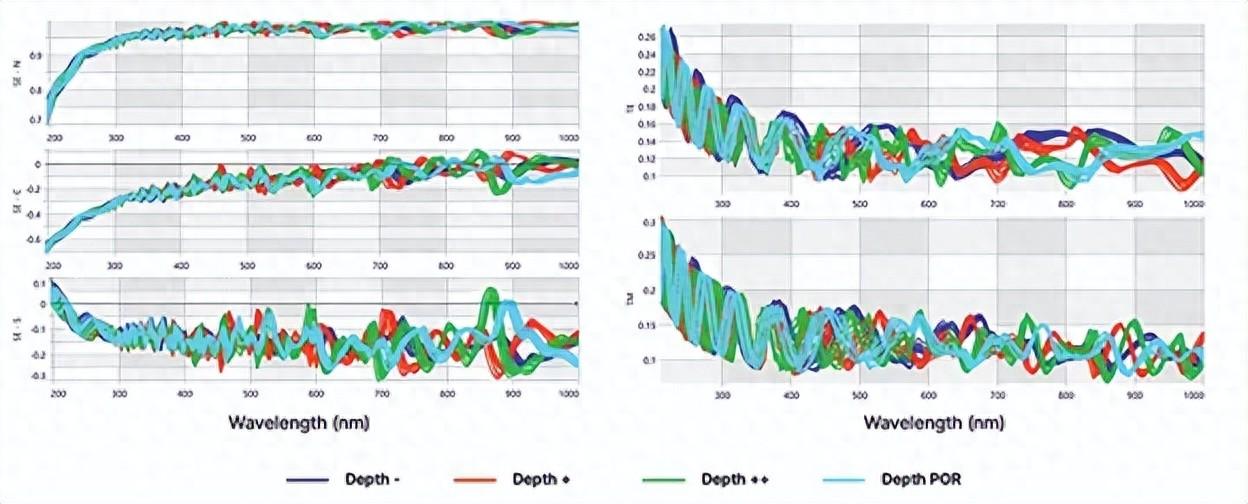
圖 1:光譜橢偏儀和正入射反射儀 OCD 通道的光譜變化。
對于我們研究中的第一個應(yīng)用,我們在四個晶圓上的溝槽蝕刻步驟中進行了實驗設(shè)計 (DOE)。改變蝕刻時間以扭曲溝槽深度。
圖 1 顯示了 SE 和法向入射反射 OCD 通道的光譜變化,按晶圓分組,具有清晰的 DOE。圖2為四片晶圓上同一位點的物理模型和模型擬合實驗結(jié)構(gòu);它還顯示平均溝槽深度與基于 DOE 條件的預(yù)期深度,具有良好的相關(guān)性。
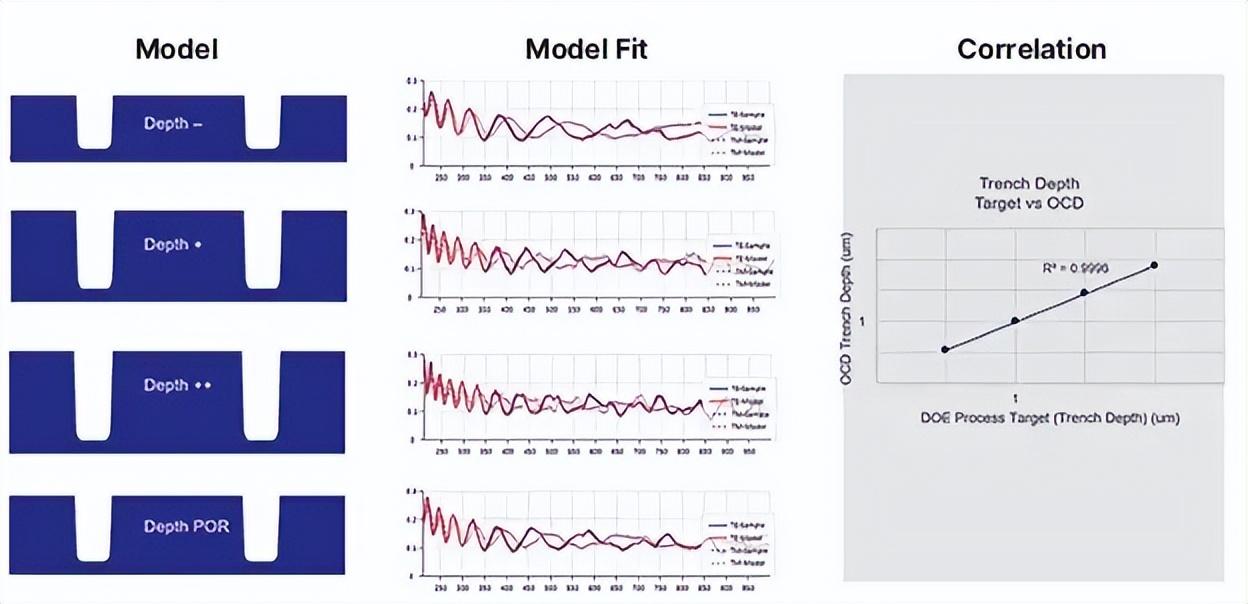
圖 2:物理模型和模型擬合四個 DOE 晶圓上的實驗結(jié)構(gòu)。
對于第二個應(yīng)用,我們擴展了上一個示例中的溝槽結(jié)構(gòu)。雖然之前的 DOE 重點關(guān)注溝槽深度,但需要考慮模型中的其他關(guān)鍵參數(shù)(包括溝槽底部寬度),因此需要進行測量。
然后,我們比較了使用單獨的 OCD 通道、SE 和 SR 以及兩個通道一起進行的模擬(圖 3)。通過結(jié)合兩個通道,我們能夠測量溝槽深度;SE 通道本身用于測量底部 CD 和頂部 CD。因此,我們確定可以使用 OCD 計量學(xué)在溝槽蝕刻步驟中測量影響器件良率和性能的所有關(guān)鍵參數(shù),包括溝槽深度以及底部和頂部 CD。
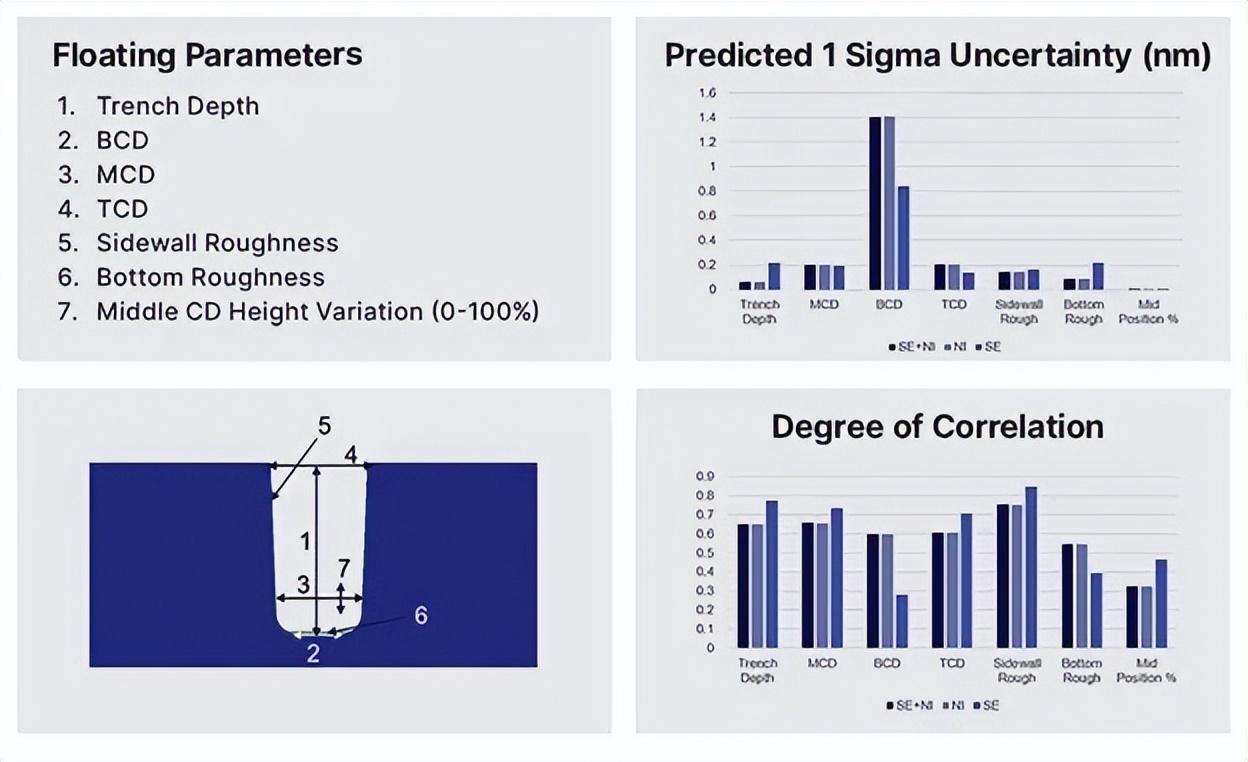
圖 3:使用光譜橢圓偏振 (SE)、正入射 (NI) 以及 SE 和 NI 組合進行的模擬比較。
使用皮秒超聲波
來優(yōu)化具有溝槽架構(gòu)的 SiC 功率器件的性能
使用皮秒超聲波
皮秒超聲波(脈沖技術(shù))是一種泵浦探測技術(shù),使用超快激光脈沖(大約 200fs)進行金屬薄膜計量;包括基于溝槽的 SiC 功率器件的金屬膜計量。
通過使用這種無損技術(shù),制造商可以同時測量多層金屬薄膜,同時還能夠區(qū)分重復(fù)金屬的各個層。對于 SiC 功率器件,皮秒超聲波為測量薄膜厚度和粗糙度提供了一種無損解決方案。
由于皮秒超聲波的優(yōu)點,它正在迅速取代更傳統(tǒng)的方法,例如四點探頭方法。其一,這些傳統(tǒng)的測量方法具有破壞性;皮秒超聲波則不然。第二,傳統(tǒng)方法不提供直接的厚度信息,并且無法檢測缺失的層或處理不當?shù)木A。
對于具有溝槽結(jié)構(gòu)的 SiC 功率 MOFET,皮秒超聲波可用于金屬化工藝控制;該應(yīng)用包括監(jiān)測接觸勢壘 (Ti/TiN)、溝槽金屬化(W 基接觸)以及正面和背面金屬化 (Ti/NiV/Ag) 堆棧。
在我們的研究中,我們測量了帶有溝槽的 SiC 功率器件中源極和漏極接觸的歐姆接觸和導(dǎo)電金屬層厚度。這些測量很重要,因為它們對接觸電阻有直接影響;接觸電阻差的功率器件將無法正常工作。金屬厚度均勻性也會對終端設(shè)備的可靠性產(chǎn)生影響。
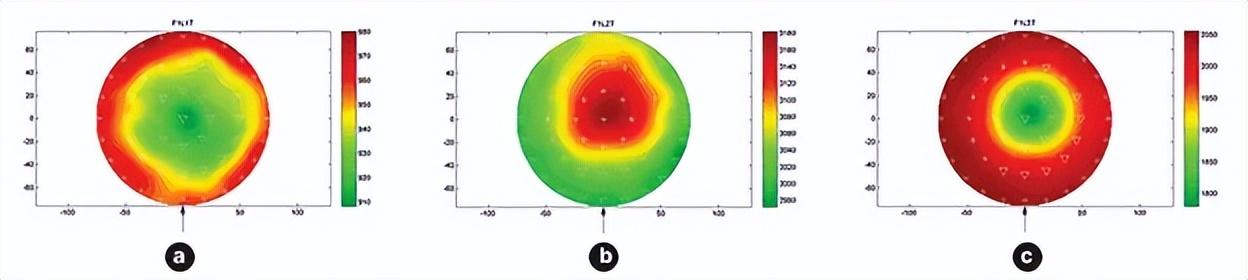
圖 1:(a) Ti 1000 ?、(b) NiV 3000 ? 和 (c) Ag 1500 ? 的 49 個點圖。
使用皮秒超聲波技術(shù),我們測量了多層金屬堆疊;在本例中,層為 Ti/NiV/Ag。由于光斑尺寸小 (8μm x10μm) 和快速測量時間(每個位置 <4 秒),我們能夠表征整個晶圓的均勻性。
此外,我們的研究中使用皮秒超聲波顯示出 3 sigma < 0.25% 標準差的出色精度。
如前所述,皮秒超聲波的主要優(yōu)點之一是能夠測量多層堆疊中的重復(fù)金屬。在本例中,我們測量了 Ti/Al/ox/Ti/Al 的堆棧,其中 Ti 重復(fù)。該技術(shù)生成的原始數(shù)據(jù)顯示出出色的信噪比,每一層的回波都清晰可見。
X 射線計量等競爭技術(shù)無法提供此類堆疊中的各個層,并且對覆蓋膜的測量并不代表產(chǎn)品性能。此外,還可以設(shè)置配方來標記丟失的層或檢測錯誤處理。
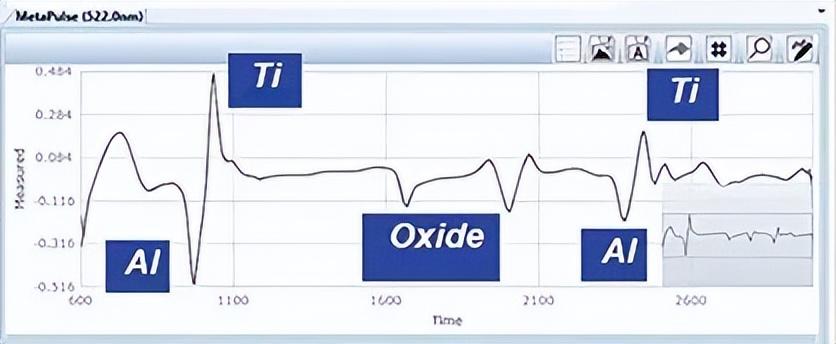
圖 2:多層金屬化堆疊測量。
除了厚度之外,皮秒超聲波還可用于監(jiān)測粗糙度,特別是厚金屬薄膜(數(shù)千埃到微米范圍)。粗糙度可作為監(jiān)控完善流程的定性指標。
圖 3 顯示了用于驗證此功能的鋁膜的測量結(jié)果。該測量結(jié)果與透射電子顯微鏡 (TEM) 和原子力顯微鏡 (AFM) 參考的相關(guān)性非常好,R 2 ~f 0.99。
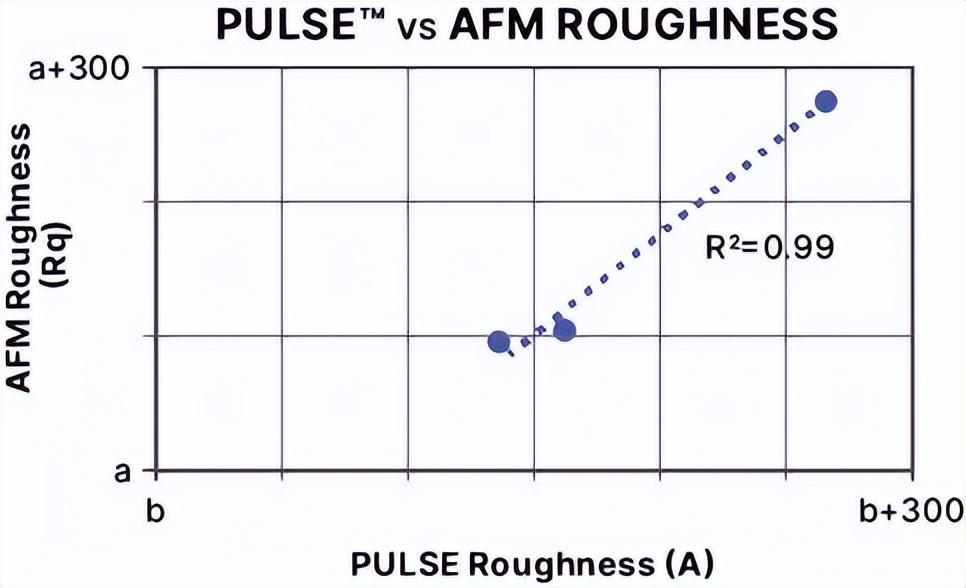
圖 3:PULSE 測量與透射電子顯微鏡 (TEM) 和原子力顯微鏡 (AFM) 的相關(guān)性。
碳化硅 (SiC) 功率器件注定將成為推動混合動力汽車和電動汽車以及其他綠色創(chuàng)新發(fā)展的主要驅(qū)動力之一。但部分由于這些 SiC 功率器件采用溝槽結(jié)構(gòu),制造商需要做好準備,以避免其過程中的許多工藝控制障礙。借助 FTIR、OCD 和皮秒超聲波計量,SiC 功率器件制造商有多種選擇能夠應(yīng)對這些挑戰(zhàn),并在此過程中為未來掃清道路。
來源: 碳化硅芯觀察
評論