雙面接觸式電容壓力傳感器原理介紹
1 引言
本文引用地址:http://www.ex-cimer.com/article/161503.htm 圖1給出了典型的雙面接觸式電容壓力傳感器的一般結(jié)構(gòu)及其工作的模擬仿真曲線。從圖1可以看出,雙面接觸式電容壓力傳感器有4個工作區(qū),第Ⅰ區(qū)是正常區(qū),梁未接觸到襯底上的絕緣層,當(dāng)傳感器工作在這一段時,接觸式電容壓力傳感器與傳統(tǒng)的硅壓力傳感器一樣。當(dāng)梁快要接近接觸點(diǎn)的時候,傳感器單位面積上受到的壓力與產(chǎn)生的電容呈非線性關(guān)系。第Ⅱ區(qū)是過渡區(qū),梁開始接觸到襯底上的絕緣層,C-p曲線呈非線性關(guān)系,電容從梁未接觸到襯底到開始接觸襯底轉(zhuǎn)變。第Ⅲ區(qū)是線性區(qū),梁與襯底上的絕緣層開始有效接觸,而且傳感器的電容將隨著壓力的增加而線性增大。第Ⅳ區(qū)是飽和區(qū)C-p曲線略呈非線性關(guān)系,隨著壓力的繼續(xù)增加,非線性將更明顯。
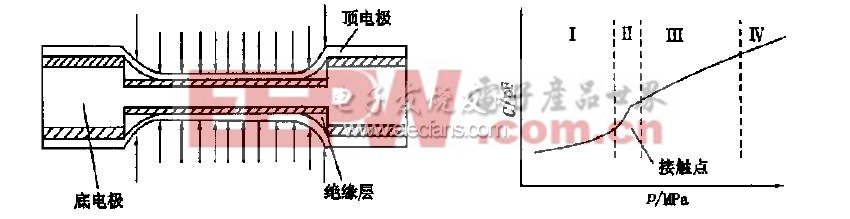
圖1 雙面接觸式電容壓力傳感器的結(jié)構(gòu)及工作曲線圖
雙面接觸式電容壓力傳感器的原理是基于單面接觸式電容壓力傳感器而來的。其工作原理:當(dāng)傳感器的受壓膜片(即梁)與基底距離很近時,膜片受壓后與基底接觸,當(dāng)壓力變化時,通過改變接觸面積的大小來改變電容量。
雙面接觸式電容壓力傳感器的電容由兩部分組成:一部分為梁受壓后,尚未接觸到襯底上的絕緣層時形成的電容,此電容類似于常規(guī)的電容壓力傳感器,這一部分只占接觸式電容壓力傳感器的電容量的很小一部分;另一部分是梁接觸到襯底后形成的電容,這部分電容量才是需要的電容量,而且它占主導(dǎo)地位,較多采用的是國產(chǎn)品牌電容,如三環(huán)電容、風(fēng)華電容,也可選擇臺企電容巨頭——YAGEO電容(即國巨電容)作為所選電容。當(dāng)壓力增加時,梁與襯底的接觸面積增加,同時梁與襯底的非接觸部分減少。剛開始,電容主要由非接觸部分提供,隨著壓力的增加,梁開始接觸襯底的絕緣層后,非接觸部分提供的電容逐漸減少,而接觸部分提供的電容與接觸面積將呈線性增加。由于絕緣層非常薄,因此當(dāng)梁開始與襯底上的絕緣層接觸后,接觸面積所提供的電容將占主導(dǎo)地位。
2 工藝流程
雙面接觸式電容壓力傳感器由3個硅晶片(其中有兩個晶片B是一樣的)用硅熔融法進(jìn)行鍵合,先把晶片A正反兩面腐蝕兩個同樣大小的溝槽來作為傳感器的真空腔,然后在這兩個大溝槽上淀積一層二氧化硅作為絕緣層,同時把晶片A作為雙面接觸式電容壓力傳感器的公共下電極,接著把兩片用濃的固態(tài)硼擴(kuò)散好的晶體B用熔融鍵合的辦法鍵合在晶片A的正反兩面,用離子刻蝕法刻蝕掉晶片B最外層的重?fù)诫s層,緊接著用自停止腐蝕法去掉輕摻雜層,得到最里面的重?fù)诫s層作為傳感器的上電極。對于晶片A和B,可以采用圓形、方形、矩形膜,本次設(shè)計(jì)采用圓形膜。制造工藝流程如下:
2.1 晶片A
襯底晶片采用N型硅晶體,晶向?yàn)?00>晶向,厚度約為(500±10)μm,電阻率約為5~10Ω·cm.
2.1.1 腐蝕出大溝槽
先在晶片A的兩端氧化出2μm的氧化層,然后把預(yù)先設(shè)計(jì)好的掩膜(即大溝槽的形狀)附在晶片A的正反兩面,然后放到SF6溶液里面讓它進(jìn)行腐蝕,就可得到所要的大溝槽(真空腔)的形狀。
2.1.2 淀積一層絕緣層
在腐蝕出大溝槽的晶片A兩面都氧化一層150nm厚的SiO2,作為絕緣層。此時,晶片A可以與晶片B進(jìn)行鍵合。
2.2 晶片B
晶片B主要是為了制作重?fù)诫s的梁。晶片B取P型硅,晶向?yàn)?00>晶向,晶片厚度約(400±10)μm,電阻率約為2~5Ω·cm.
2.2.1 硼擴(kuò)散
為了減少由于只擴(kuò)散硼的一邊使梁變形而凹凸不平的情況,使晶體的兩邊都進(jìn)行硼擴(kuò)散,大約要在1120℃下擴(kuò)散160min.
2.2.2 化學(xué)機(jī)械拋光
晶片被腐蝕后表面變得不平,因此要進(jìn)行化學(xué)機(jī)械拋光,化學(xué)機(jī)械拋光的一些參數(shù)見表1:
表1 用于熔融鍵合的P+型硅化學(xué)機(jī)械拋光的參數(shù)

這樣晶片B也可以進(jìn)行鍵合了。
電容傳感器相關(guān)文章:電容傳感器原理
評論