基于計算機輔助設計技術(TCAD)的工藝開發(fā)
隨著半導體工藝開發(fā)和制造成本的快速上升和復雜程度不斷加深,半導體制造商如今面臨著前所未有的挑戰(zhàn)。為了滿足成本更低和功能更多的產(chǎn)品需求,半導體工藝的更新?lián)Q代取決于不同器件類型的升級和集成——核心邏輯金屬-氧場效晶體管(MOSFETs),嵌入式閃存,高壓器件等——需要對制造設備和晶圓試驗測試進行巨額投資才能實現(xiàn)工藝目標。而且,一旦新工藝投入制造,盡快實現(xiàn)制造良品率達到盡可能高的水平則變得越來越重要,甚至要保證采用新工藝制造的產(chǎn)品的獲利能力。
本文引用地址:http://www.ex-cimer.com/article/202500.htm為幫助減輕這些挑戰(zhàn),東芝已經(jīng)開發(fā)出基于模擬的技術實現(xiàn)良率的快速提升,并減少工藝開發(fā)成本和時間。該方法在技術生命周期的各個階段,從開發(fā)到制造,都依賴工藝和器件模擬軟件的應用,即計算機輔助設計技術(TCAD)。這種技術適用性強,可以應用到其它半導體制造環(huán)境當中。
方法描述
計算機輔助設計技術(TCAD)方法依賴于特征尺度形貌模擬器Sentaurus Topography和硅工藝模擬器Sentaurus Process,其中包括三個階段。
1. 工藝開發(fā)概念的設計和選擇
2. 概念選擇
3. 對批量生產(chǎn)進行工藝優(yōu)化
開發(fā)工藝流程的第一階段是對開發(fā)概念的設計和制定,移除無效工藝步驟和失效(或危險)的晶格。確認這些“危險晶格”對建立一個初始工藝流程至關重要,并為進一步優(yōu)化打下堅實的基礎。
這個確認過程是通過使用工藝模擬工具二維器件形狀(Device D-2)來完成的,橫截面形狀通過形貌模擬器進行模擬,溫度步驟如擴散和氧化過程則由工藝模擬器來完成。一旦整個工藝的輪廓制定完成,代表晶格被移除并核對,對這些晶格的橫截面視圖是否存在故障進行檢查。
下一步驟開始進行晶圓測試,并對物理模型進行校準。對工藝流程變量進行優(yōu)化,使該流程可以更適應制造過程中出現(xiàn)的變化。在最后階段投入批量生產(chǎn)時,工藝流程的重點再次回到使用從生產(chǎn)環(huán)節(jié)獲得的質量控制數(shù)據(jù)進行模擬,這些數(shù)據(jù)包括蝕刻速率、沉積率、氧化條件等,這些將被作為模擬器的輸入數(shù)據(jù)。
通過這個方法,結合移除所謂的危險晶格,以及容易導致故障的工藝,減少檢驗工藝流程所需要的試驗分裂條件數(shù)量,可以明顯地減少開發(fā)時間,同時提供更適用的工藝進行批量生產(chǎn)。其結果就是:優(yōu)化良率。
開發(fā)和制造階段
圖1為第一階段移除危險工藝步驟和晶格。首先,用戶確定獲得橫截面視圖的位置。如A-A’或E-E’。
器件版圖(左上圖)及對其不同橫截面進行分析(右側)。底部為工藝流程。
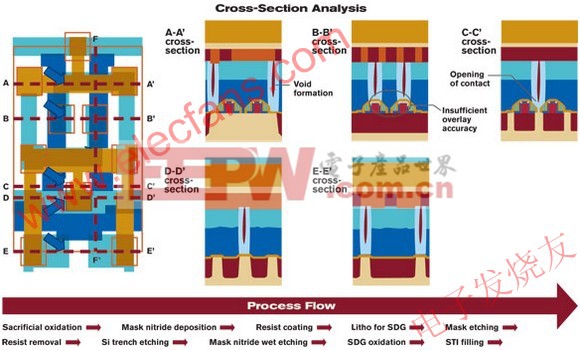
圖1.器件版圖(左上圖)及對其不同橫截面進行分析(右側)。底部為工藝流程。
在給定工藝流程和所選擇位置使用計算機輔助設計技術(TCAD)工具,通過觀測檢查每個晶格模擬結果的不同橫截面視圖。例如,在A-A’橫截面的接觸處形成孔隙;在B-B’ 橫截面的接觸處,在柵與接觸之間對準精度不足可能導致失效;以及在C-C’橫截面的接觸開口處顯然可能出現(xiàn)失效。
如圖2所示,一旦工藝流程變的更加具體,對目標工藝流程中不同晶格的許多橫截面視圖進行系統(tǒng)檢查,可使用自動建立和生成許多結構,這些結構可以覆蓋大量的器件類型所使用的尖端工藝:n- 和p- 通道金屬氧化物半導體(MOS)晶體管、嵌入式內存、輸入/輸出器件等。如果不能自動生成結構,則幾乎不可能手動建立和模擬所需橫截面視圖。
為過濾危險晶格,計算機輔助設計技術(TCAD)工具可最多對代表晶格的截面通過最多150個工藝步驟對晶粒X進行系統(tǒng)檢測,這幾乎是手動所無法完成的。

圖2.為過濾危險晶格,計算機輔助設計技術(TCAD)工具可最多對代表晶格的截面通過最多150個工藝步驟對晶粒X進行系統(tǒng)檢測,這幾乎是手動所無法完成的。
評論